W szybko rozwijającym się świecie elektroniki rośnie zapotrzebowanie na wysokowydajne wielowarstwowe płytki PCB typu Rigid-Flex. Te zaawansowane płytki drukowane łączą w sobie zalety sztywnych i elastycznych płytek PCB, umożliwiając tworzenie innowacyjnych projektów, które można zmieścić w niewielkich przestrzeniach, zachowując jednocześnie wysoką niezawodność i wydajność. Jako wiodący producent wielowarstwowych płytek PCB, firma Capel Technology rozumie zawiłości związane z projektowaniem i produkcją tych złożonych płytek. W tym artykule omówiono metody optymalizacji projektowania obwodów w wielowarstwowych sztywnych i elastycznych płytkach drukowanych, zapewniając spełnienie rygorystycznych wymagań nowoczesnych aplikacji elektronicznych.
1. Rozsądne ustawienie odstępów między liniami drukowanymi na komponentach
Jednym z głównych czynników branych pod uwagę przy projektowaniu wielowarstwowych płytek PCB typu Rigid-Flex jest odstęp pomiędzy drukowanymi liniami i komponentami. Odstęp ten ma kluczowe znaczenie dla zapewnienia izolacji elektrycznej i dostosowania procesu produkcyjnego. Jeżeli na tej samej płytce znajdują się obwody wysokiego i niskiego napięcia, istotne jest zachowanie wystarczającej odległości bezpieczeństwa, aby zapobiec zakłóceniom elektrycznym i potencjalnym awariom. Projektanci muszą dokładnie ocenić poziomy napięcia i wymaganą izolację, aby określić optymalny odstęp, zapewniający bezpieczne i wydajne działanie płytki.
2. Wybór typu linii
Na aspekty estetyczne i funkcjonalne płytki PCB duży wpływ ma wybór rodzaju linii. W przypadku wielowarstwowych płytek PCB typu Rigid-Flex należy zachować ostrożność przy wyborze układu narożników przewodów i ogólnego rodzaju linii. Typowe opcje obejmują kąty 45 stopni, kąty 90 stopni i łuki. Generalnie unika się ostrych kątów ze względu na ich potencjał tworzenia punktów naprężeń, które mogą prowadzić do uszkodzeń podczas zginania lub zginania. Zamiast tego projektanci powinni preferować przejścia łukowe lub przejścia pod kątem 45 stopni, które nie tylko poprawiają możliwości produkcyjne płytki drukowanej, ale także przyczyniają się do jej atrakcyjności wizualnej.
3. Wyznaczanie szerokości linii drukowanej
Szerokość linii drukowanych na wielowarstwowej płytce PCB Rigid-Flex to kolejny krytyczny czynnik wpływający na wydajność. Szerokość linii należy określić na podstawie poziomu prądu, jaki będą przewodzić przewodniki, oraz ich odporności na zakłócenia. Ogólna zasada jest taka, że im większy prąd, tym szersza powinna być linia. Jest to szczególnie ważne w przypadku linii zasilających i uziemiających, które powinny być jak najgrubsze, aby zapewnić stabilność kształtu fali i zminimalizować spadki napięcia. Optymalizując szerokość linii, projektanci mogą poprawić ogólną wydajność i niezawodność płytki drukowanej.
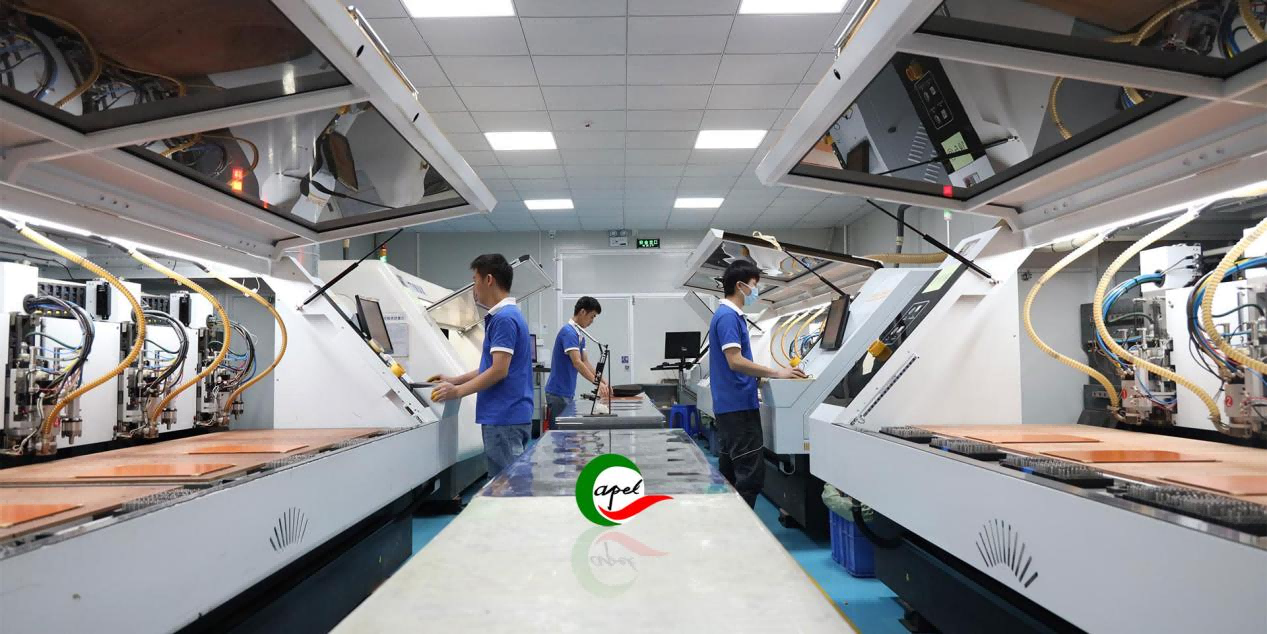
4. Ekranowanie przeciwzakłóceniowe i elektromagnetyczne
W dzisiejszych środowiskach elektronicznych o wysokiej częstotliwości zakłócenia mogą znacząco wpłynąć na działanie płytki drukowanej. Dlatego przy projektowaniu wielowarstwowych płytek PCB typu Rigid-Flex niezbędne są skuteczne strategie przeciwzakłóceniowe i ekranowania elektromagnetycznego. Przemyślany układ obwodów w połączeniu z odpowiednimi sposobami uziemienia może znacząco ograniczyć źródła zakłóceń i poprawić kompatybilność elektromagnetyczną. W przypadku krytycznych linii sygnałowych, takich jak sygnały zegara, zaleca się użycie szerszych ścieżek i zastosowanie uszczelnionych przewodów uziemiających do owijania i izolacji. Takie podejście nie tylko chroni wrażliwe sygnały, ale także zwiększa ogólną integralność obwodu.
5. Projekt strefy przejściowej sztywna-elastyczna
Strefa przejściowa pomiędzy sztywną i elastyczną sekcją płytki drukowanej Rigid-Flex to krytyczny obszar wymagający starannego zaprojektowania. Linie w tej strefie powinny przechodzić płynnie, a ich kierunek jest prostopadły do kierunku zgięcia. To rozwiązanie konstrukcyjne pomaga zminimalizować naprężenia działające na przewody podczas zginania, zmniejszając ryzyko awarii. Dodatkowo szerokość przewodów powinna być zmaksymalizowana w całej strefie zginania, aby zapewnić optymalną wydajność. Ważne jest również, aby unikać otworów przelotowych w obszarach narażonych na zginanie, ponieważ mogą one spowodować powstanie słabych punktów. Aby jeszcze bardziej zwiększyć niezawodność, projektanci mogą dodać ochronne przewody miedziane po obu stronach linii, zapewniając dodatkowe wsparcie i ekranowanie.
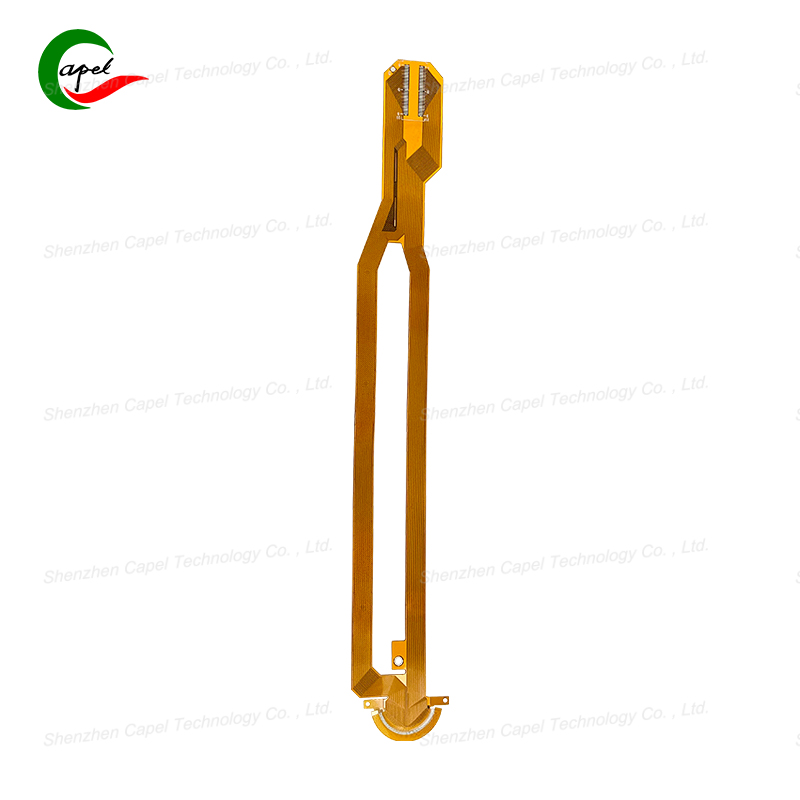
Czas publikacji: 12 listopada 2024 r
Z powrotem